Melissa Ma
Junior Mechanical Engineering Student @ University of Toronto | Engineering with a Purpose
Feel free to zoom in/out for better viewing experience of website!
Remote Car
*Work in Progress*
​
Fusion360 | 3D Printer | Power Tools
The goal is to design an RC car from scratch because I want to learn about how cars work (and also to reinforce understanding of mechanical mechanisms learned in class).
​

Solidworks Render

3D printed gears for transmission and steering mechanism

Cardboard cutouts for steering mechanism (Parallel Motion (Push/Pull) linkage)
3D printed gears for transmission and steering mechanism
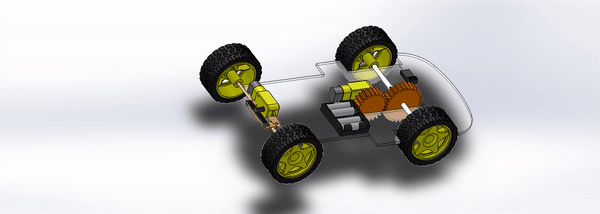
Steering mechanism (parallel linkage) animation

Chassis
The chassis needed some re-engineering to accommodate the motor, transmission, and steering assemblies
Transmitter, receiver, battery, and motor circuit (1 channel)
Transmission mechanism demo (1st channel)
Steering mechanism demo (2nd channel)
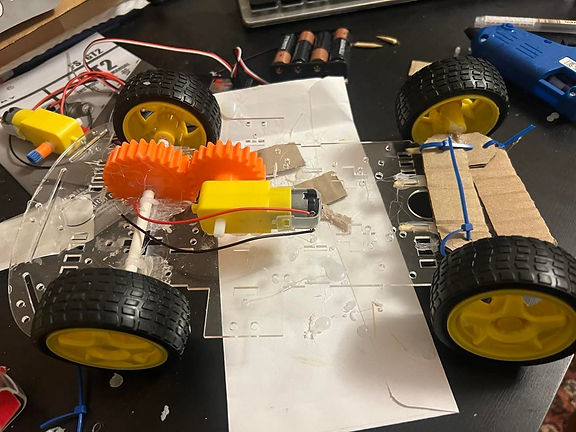
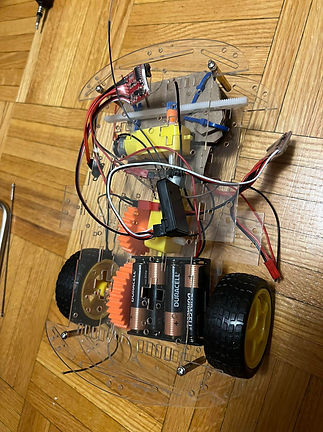
Steering assembly attached but needs some modification
(wheels are wobbly)

Transmission assembly attached to chassis. It uses a 24-teeth driver gear that is mounted on the DC motor. This gear further drives a 30-teeth output gear that drives the axle. This gear ratio increases the torque of the car.
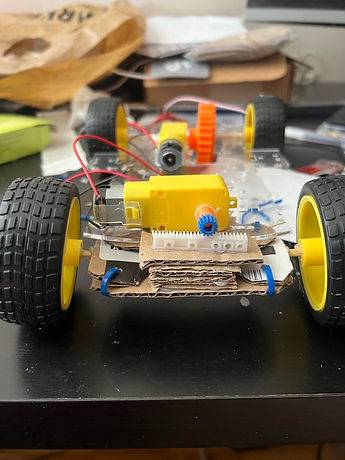
Steering assembly uses a rack and pinion mechanism
to drive a parallel motion linkage, which drives the rear wheels.
Role
​Mechanical Designer | Electrical Engineer | Technician
Project Highlights
-
Designed parts of the system in Fusion360 (gears and shafts for the transmission)
-
Used ESC, transmitter, receiver, DC motors, rack&pinion, 3D printed gears, and power tools to build the car
-
Wired receiver & transmitter circuit
Tools
Fusion360 | 3D Printer | Power Tools
Results/Lessons Learned
-
Always design for tolerance!!!!
-
Find creative solutions to redesign/re-engineer a component (given that it is cost-effective, non-time-extensive, and doesn't breach the component's functions/objectives/constraints. For example, when the gears I printed didn't have enough tolerance to fit the motor shaft, I heated the gear with a lighter and while it is semi-soft, I pushed the gear into the shaft to make it conform to the right geometry. This saved me printing time and cost.
-
Always check for multiple supplier channels - got components for too high of a price in a robotics store VS. cheaper on Amazon
-
YouTube and online tutorials are super helpful when you don't know how to use a part. For example, I did not know how to wire up the ESC to the receiver/transmitter circuit at all. Luckily, I found useful tutorials that taught me what the different channels do and what polarity each of the wires corresponded to.
-
I got to practice my soldering skills a lot more too, since I had to solder all the wires in my receiver circuit.
-
When gluing things together, bear in mind which components move TOGETHER and which ones move INDEPENDENTLY! For instance, when I was gluing the axle+wheels sub-assembly to the car, I overlooked the fact that the axle needs to rotate about an axis independently, in order to drive rotary motion from the wheels.
​
​