Melissa Ma
Junior Mechanical Engineering Student @ University of Toronto | Engineering with a Purpose
Feel free to zoom in/out for better viewing experience of website!
Alstom/Bombardier
(Project Engineering Intern)
Highlights
-
Used CATIA V5 (part design & generative shape design) to route complex steel pipes for air intake systems that are to be installed on 20 trains under Go Transit
-
Drafted 10+ toleranced engineering drawings of pipes and complex geometries, which were successfully used in the manufacturing process
-
Sourced parts to create mockups and prototypes for conduit systems (fittings, pipes, conduit brackets etc) from hardware stores and McMaster-Car
-
Utilized project management software (Excel, PowerBI) to streamline project progress and sales forecasts; created pivot tables to reflect KPIs
-
Worked with internal customers, suppliers, and technicians by overseeing prototyping creation processes, taking meeting notes in project kickoff meetings, discussing project timelines with customers, and calling suppliers to discuss manufacturing details
-
Reviewed 20+ project initiation, engineering proposals, engineering instructions, commercial proposal, cost sheet, inventory, quality assurance, maintenance procedure, quality audits, and risk assessment documents
Design problem: reroute the transmission hot start coolant pipe (red arrow) so it doesn't interfere with the pre-cleaner box (blue arrow, it filters out snow and clumps during winter to ensure safety and reliability) and other pipes around it

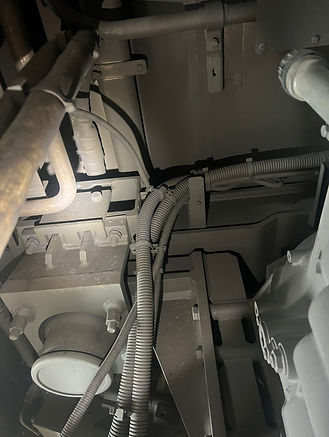
Spare transmission system
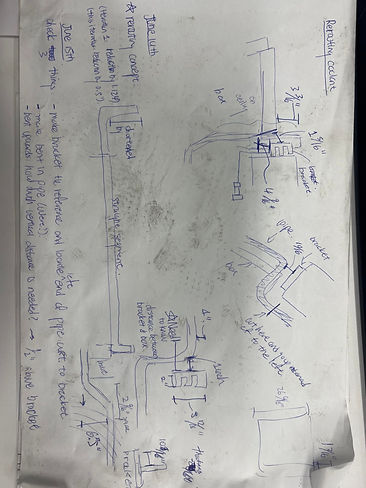
After taking many measurements under the train (by doing acrobatics and squeezing between things), I pinpointed the areas where we had to adjust for tolerance
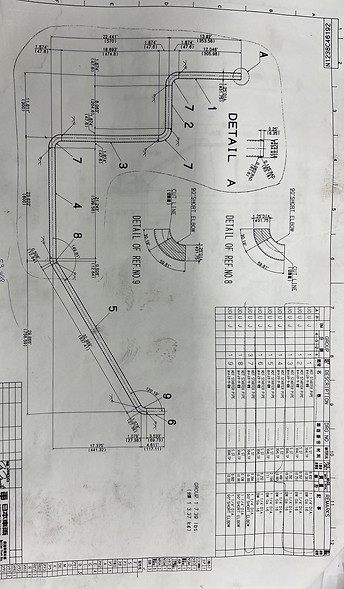
Original pipe design


Pipe design in CATIA V5


Prototype (white pipe) installed on spare transmission system. I sourced the abs pipes and fittings from Home Depot. When designing the pipe, important factors such as movement due to vibration, maintenance, and laminar/turbluent fluid flow due to different bend radii are taken into account.


Important design practice that I learned: when taking measurements of such a pipe geometry we should use the origin as the reference point and take x,y,z distance measurements from that point. This is because if we were to take measurements from different reference points (for example, initially I was taking each succeeding pipe segment's length and bend angle with respect to the previous segment - see Method 1 vs Method 2, both not to scale).
Results/Lessons Learned
​​
​
​
Drawing was sent to the manufactuer and 20 pipes are expected to be installed in September 2022!
Method 1



Method 2
Door Trim Drawing Sent to Supplier

Pipe Drawing Sent to Supplier

Transmission assembly in CATIA V5:
-
To familiarize myself with how a transmission works, I assembled a transmission system in CATIA V5
-
The purpose of a transmission system is to convert energy from the engine into energy for the wheels​
-
-
Parts include ball bearing, conic roller bearings, pinion mechanism, bevel gear, crown wheel, gear axles, etc.


Solidworks rendering of the transmission system
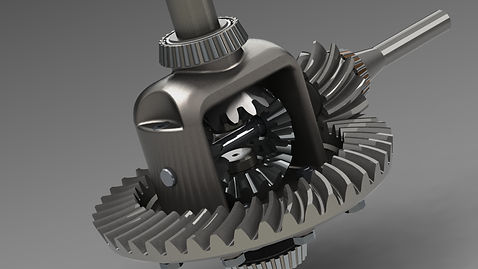

CATIA Surface modelling:
-
I utilized CATIA surface modelling to model a sedan:
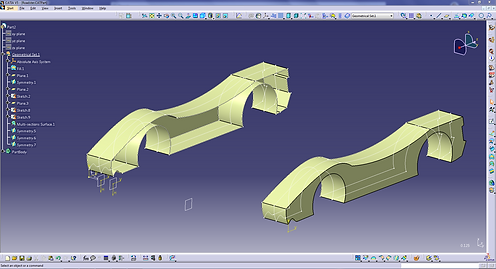

GD&T: A tolerancing practice that tells us the function of a design, in addition to the dimensional requirements. In this way, the
manufacturer would be able to better understand the design requirements when they make the part.
Mechanical Bill of Materials (BOMs): During my internship at Alstom, I got to review some mechanical BOMS for various projects
and perform relevant calculations.
Project Lifecycle: During a project's life cycle, we need a systematic approach to keep track of the project progress through
various documents
-
Project initiation/proposal
-
Engineering proposal
-
Project Plan
-
Engineering Instructions
-
Commercial Proposal
-
ATCWS
-
QA
-
Production